Enhancing Your Welding WPS: Strategies for Improved Performance and Performance
Enhancing Your Welding WPS: Strategies for Improved Performance and Performance
Blog Article
Grasping Welding WPS Criteria: Best Practices and Techniques for High Quality Welds
In the realm of welding, mastering Welding Treatment Spec (WPS) criteria is an important component that straight affects the high quality and stability of welds. Sticking to these standards ensures uniformity and dependability in welding outcomes. Nonetheless, accomplishing quality in welds exceeds just recognizing the criteria; it entails implementing best practices and strategies that boost the craft to a level of precision and skill that establishes apart the standard from the exceptional. As we navigate via the complexities of welding WPS criteria, revealing key insights and approaches for attaining top-tier welds will certainly be vital for welders looking for to master their craft and produce welds that stand the examination of time.
Comprehending Welding WPS Criteria

Inspectors rely on WPS paperwork to verify that welding treatments are being adhered to correctly and that the resulting welds are of high quality. Engineers utilize WPS requirements to create welding treatments that make sure the durability and integrity of bonded frameworks.
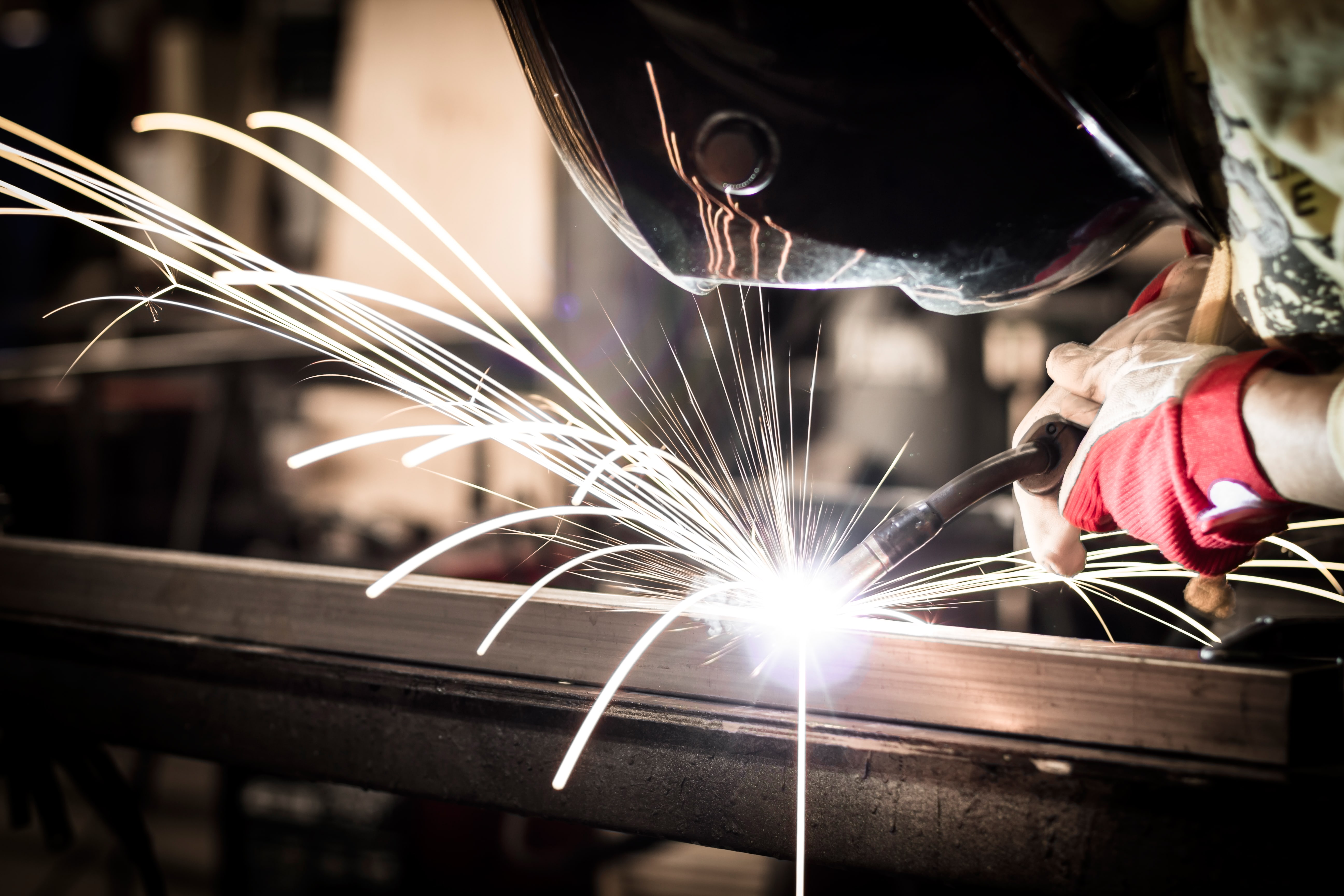

Vital Tools for Top Quality Welds
Mastering welding WPS criteria is crucial for welders to effectively make use of the essential tools required for generating high quality welds. Among one of the most critical tools for top quality welds is a welding machine. The sort of welding equipment required depends on the welding process being utilized, such as MIG, TIG, or stick welding. Welding safety helmets are also important to protect the welder's eyes and face from sparks, warmth, and UV radiation. In addition, welding gloves made of heat-resistant and resilient products protect the hands from injuries and burns. Magnets and clamps assist hold the work surfaces with each other securely throughout the welding procedure, making sure exact and precise welds. Cord brushes and damaging hammers are essential for cleaning the weld joint before and after welding to eliminate any pollutants that could influence the top quality of the weld. Finally, a determining tape and angle grinder serve devices for making sure correct placement and preparing the workpieces for welding.
Trick Strategies for Welding Success
To achieve welding success, one should grasp the key methods vital for producing top notch welds. Maintaining a stable welding and a consistent hand setting throughout the procedure is vital to achieving precision and uniformity in the welds. By grasping these crucial methods, welders can boost the high quality of their work and achieve welding pop over to these guys success.
Ensuring Compliance With WPS Requirements
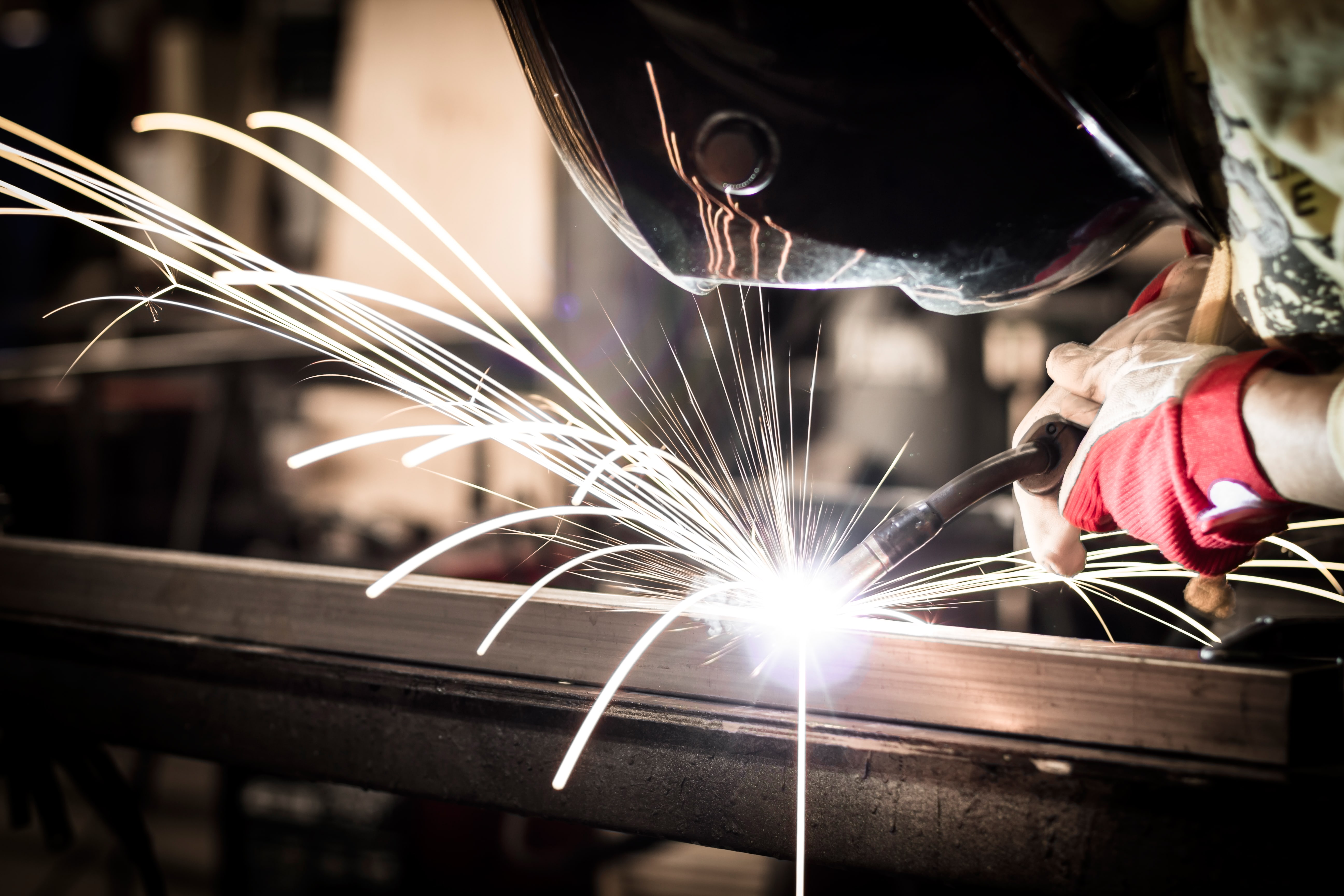
In addition, welders should go through training to familiarize themselves with the WPS requirements pertinent to their job. Routine audits and evaluations must be carried out to verify that welding tasks straighten with the suggested WPS standards. Additionally, keeping in-depth documents of welding parameters, equipment calibration, and inspection outcomes is crucial for showing conformity with WPS criteria - welding WPS. By carefully sticking to WPS requirements, welders can make certain that their work meets the needed quality levels and adds to the overall success of the welding task.
Troubleshooting Common Welding Issues
When confronted with usual welding issues, determining the source is essential for reliable troubleshooting. One prevalent trouble is the presence of porosity in welds, often created by impurities such as rust, oil, or wetness. To address this, making certain proper cleansing of the base metal before welding and using the right protecting gas can substantially decrease porosity. One more concern often run into is absence of fusion, where the weld stops working to properly bond with the base material. This can come from insufficient heat input or improper welding method. Readjusting specifications such as voltage, wire feed rate, or More Info travel rate can assist improve blend. Furthermore, distortion, cracking, and spatter are typical welding obstacles that can be alleviated via correct joint preparation, constant warmth control, and choosing the proper welding consumables. By extensively recognizing these typical welding concerns and their source, welders can successfully repair issues and accomplish premium welds.
Final Thought
In conclusion, understanding welding WPS requirements calls for a thorough understanding of the guidelines, making use of essential tools, and executing crucial techniques for my explanation effective welds. Guaranteeing conformity with WPS standards is critical for creating high quality welds and staying clear of common welding problems. By complying with finest strategies and methods, welders can achieve regular and reliable lead to their welding tasks.
In the realm of welding, understanding Welding Treatment Requirements (WPS) standards is a critical element that directly influences the quality and honesty of welds.When delving right into the world of welding practices, a critical aspect to comprehend is the significance and ins and outs of Welding Treatment Requirements (WPS) requirements. WPS requirements give an in-depth standard for welding operations, ensuring consistency, high quality, and safety in the welding process. The kind of welding equipment required depends on the welding procedure being made use of, such as MIG, TIG, or stick welding.Achieving welding success with the mastery of key strategies requires a detailed understanding and adherence to Welding Treatment Specification (WPS) requirements.
Report this page